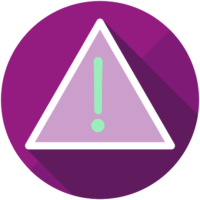
Process Failure Mode and Effects Analysis (FMEA)
Programme Overview
FMEA is a risk management and mitigation approach that began in the aerospace and engineering fields but has moved into general business and organisational practice. It is a way of thinking and methodology that can help with continuous improvement of all functional areas of an organisation, at all levels and in all sectors. This course is focused on FMEA for Process risks. We also have a Design FMEA course.
In-Company Training
Group Discount
Any work we carry out, any process we operate or product or service we provide is accompanied by risk of failure. To improve our processes, products and services, and to make them more robust and reliable, we need to identify these risks, prioritise them and then take action to mitigate and control them.
At A Glance
Failure Mode and Effects Analysis (FMEA) | |
Now Showing | Failure Mode and Effects Analysis (FMEA) |
Price | £ P.O.A (plus VAT) |
Duration | In Company: 2 days |
CPD Points | 24 |
Accreditations | TBA |
Prerequisites | None |
Delivery Modes | In-Company |
Delivered By | Gillian Rhodes, Kirsty Hutchison |
FMEA provides a structured approach which helps:
- Identify the areas and ways in which a process, system, product or service can fail (Failure Modes), the possible causes, how they might impact the customer or the business and whether there are controls in place to prevent or detect the failure mode or cause
- Prioritise the risks and plan actions to address the failure modes which are of the greatest concern
- Implement control plans to prevent recurrence of the failure modes
This one or two-day activity-based course will give you an introduction to FMEA concepts and practices, help you understand how it works and see what it can do for you organisation
Who is the course for?
- You are a leader or a team who would like to learn how FMEA could be used to help improve the processes in your organisation
- You would like to learn how to effectively generate an FMEA with a team
- You have been asked by a customer to provide an FMEA for your process but don’t know where to start or how to make it happen
- You are from a service, manufacturing or public service organisation.
Learning Outcomes
- Understand how Failure Modes and Effects Analysis (FMEA) can be used to improve your products and help make them more robust and reliable
- Learn how FMEA links to other continuous improvement tools
- Recognise how FMEA would help improve your organisation
- If you are using an Agile development approach, recognise how the FMEA way of thinking can work with Agile.
- Learn the steps necessary to work through an FMEA
Outcomes for your business
Businesses which have used FMEA to identify and mitigate the risks in their processes are likely to –
- Have more robust and reliable processes
- Have lower failure-related costs (such as rework, redesign, recalls)
- Produce fewer errors or defects
- Have fewer customer complaints
- Experience fewer safety incidents.
Outcomes for your personal development
You will learn how to use FMEA to identify and prioritise risks and improvement opportunities in the products for which you are responsible.
Prerequisites
None – this course assumes no prior knowledge of FMEA.
How can I take this course?
We deliver this course as a one or two-day in-house programme (virtual or face-to-face)
Support Pack
All delegates receive
- Printed and pdf copies of the course slides
- Blank FMEA templates which can be customised for your use
Why Choose Catalyst
- Catalyst’s instructors have hands-on experience of creating FMEAs in many different organisations, using a simple, interactive, team-based approach – we can help you consider how to use FMEA efficiently and effectively in your organisation
- We have experience of both Process FMEA and Design FMEA and can help you recognise which of these will help you improve your organisation
- We have experience of using FMEA with Agile development
- Our courses are highly interactive and use relevant examples and case studies
Contents
- Risk management
- What is an FMEA?
- Where and When to use it?
- Who prepares it and Why?
- Process FMEA strategy
- Combining a process map with FMEA
- Basic FMEA template and Cause & Effect diagrams
- Failure Modes and Effects on Customers
- Rating scales
- What are the issues when assessing risk?
- Prioritising risks using the Risk Priority Number (RPN)
- Hierarchy of Controls
- Poka Yoke/Mistake proofing systems
- Creative thinking tools and approaches
- Team composition and roles
- FMEA tips
Discover Our Failure Mode and Effects Analysis Programme for Yourself
Failure Mode and Effects Analysis (FMEA) - Our Clients' View
Our clients tell us we are
Consistently Excellent!
We’ve been using the industry standard NPS to measure customer satisfaction for over 5 years. Feedback is consistently excellent with delegates scoring an average of 9 (out of 10).