The benefits of Lean Six Sigma training are many and varied. Think quality improvements, cost savings, taking time out of processes and improving customer satisfaction. Think also about improved knowledge and capability, Black Belt, Green Belt and Yellow Belt certifications and the abundance of learning that comes from the application of Lean Six Sigma in an improvement project. In addition to all of these are a number of unexpected benefits of Lean Six Sigma training.
You become a life-long problem solver
Once learned, the DMAIC roadmap for process improvement and problem solving becomes ingrained as a means to tackle issues, address obstacles and think about things clearly. For this reason it has been used by people wishing to lose weight, improve performance in sport, advance their careers and improve their wellbeing.
The DMAIC phases – Defining problems and their impact clearly; measuring and understanding the current situation; analysing to identify root causes, developing solutions; implementing and embedding the solutions to hold the gain – provide an enduring guide for life as well as for process improvements!
Likewise, the tools and techniques of Lean Six Sigma can be applied individually – not always as part of a project or as part of a sequence. For example, using a fishbone analysis to explore the cause of a customer complaint or service failure, using a negative brainstorm to transform team meetings, or using Control Charts to understand performance results over time.
You get the importance of Change Management
Change Management absolutely underpins Lean Six Sigma, and another unexpected benefit of Lean Six Sigma training is the opportunity to learn about this vital aspect of process improvement / making things happen. Working through each DMAIC phase during training provides the opportunity to consider the responses and reactions of stakeholders and to develop plans to ensure that the changes successfully deliver anticipated results.
The E = Q x A formula for the effectiveness of change (where effectiveness is the result of quality multiplied by acceptance) is often a revelation to our learners. Building acceptance at every stage of a Lean Six Sigma project then becomes a critical focus. And as above, these insights can be applied in many situations.

And another benefit of Lean Six Sigma training – You catch fire!
When we deliver Lean Six Sigma training, sharing the principles, the roadmap and the tools and techniques with learners is not the sole objective. What we really want is to light a fire in people – inspire and motivate them to go and make a difference in their work.
We see it ignite when people practice a tool or technique that works, challenge current thinking, when statistical analysis floats their boat, or when they use creative thinking techniques to come up with a stellar solution to a longstanding problem. Or when they stand up at the flipchart to facilitate a technique for the first time and win at it. From here, people find opportunities to apply their learning in lots of different places, lighting fires as they go.
You learn a new language
It’s a fact that Lean Six Sigma comes with many TLAs and FLAs and even some SLAs! Lots of people tell us, “I’ve heard people talking about <SIPOCs / Gauge R&Rs / CTQs / FLOTs/etc> and I’ve never known what they were talking about until now!”
Wait a second. FLOTs? I made that one up! Which leads on to another unexpected benefit of Lean Six Sigma training – Lean Six Sigma humour. How we chuckle when we see a funny shaped distribution curve, ponder over Deming’s two word message to management, and suggest alternative layouts to the office canteen after learning about Spaghetti Mapping. And then there’s the all-time classic…the glass is neither half full nor half empty: it’s twice as big as it needs to be. Oh the hilarity.
But one of the most important benefits of Lean Six Sigma training is understanding how to apply the tools and concepts and to explain these things to colleagues in plain, clear language that means something to them and helps get the work done.
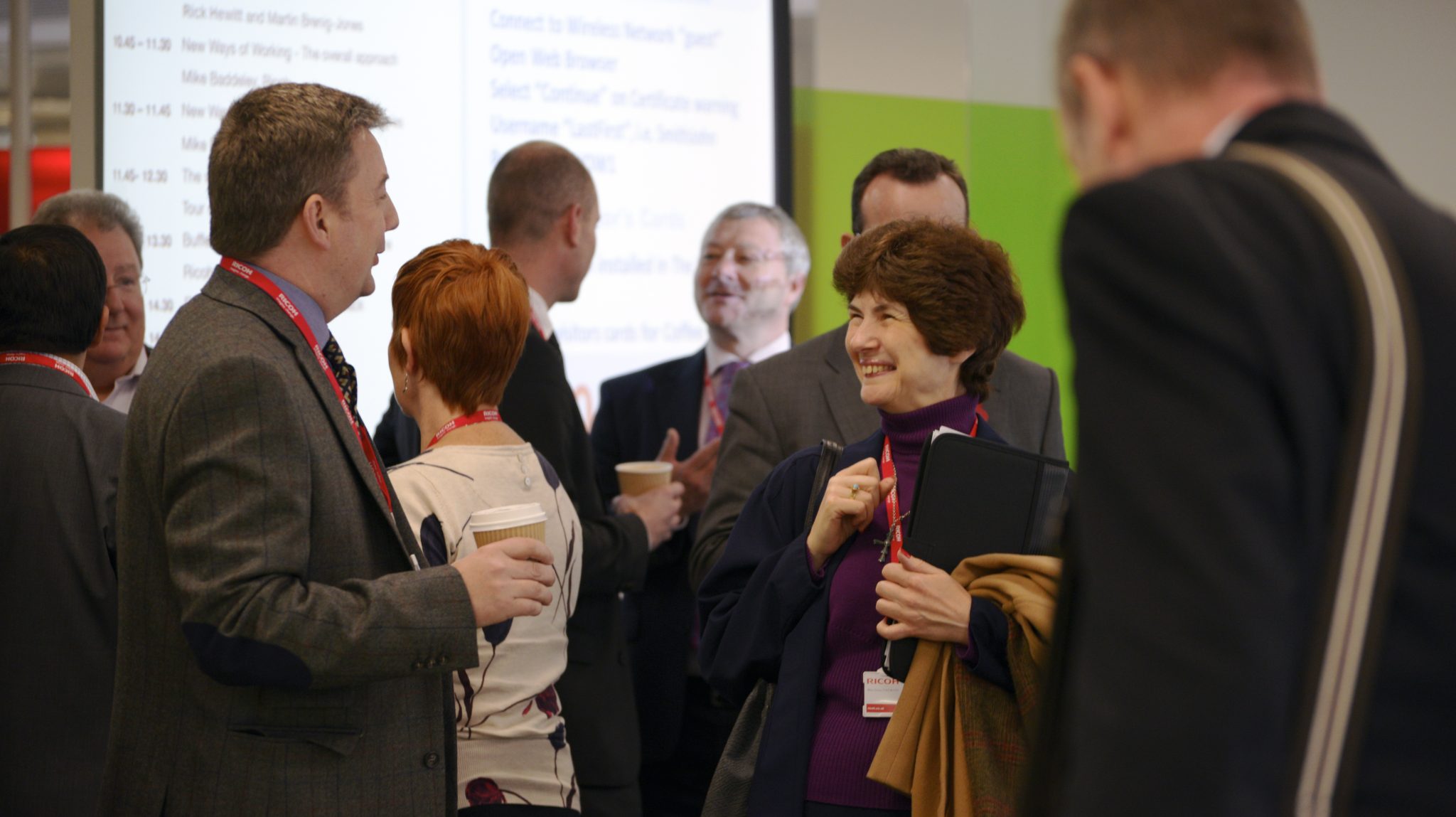
You’re part of a network
At Catalyst we regularly host Deployment Leaders’ Network days to share experience, advice and the latest best practices. Linking up with a network of people who’ve had Lean Six Sigma training inside or outside of your organisation can provide you with the opportunity to do this closer to home. It can also be done by keeping in touch with classmates you meet in the training, or via social media platforms. There’s lots to be learned from networking and many benefits associated with developing a network.
Lifelong learning is defined as the ongoing, voluntary and self-motivated pursuit of knowledge for personal or professional reasons, that enhances social inclusion, active citizenship and personal development, also self-sustainability, competitiveness and employability. These are very real benefits of Lean Six Sigma training and its application.
Jo is a motivated and energetic business improver with extensive experience in developing and deploying Continuous Improvement, Lean Six Sigma, ISO and Excellence strategies across a broad range of organisations and sectors.