Of all the quotes about beginnings, fresh starts and the joy of something new, this one from David DeNotaris seems most appropriate when it comes to starting a new Lean Six Sigma project:
“Dissatisfaction is a great starting point, for it is right there that we have the most power, strength and energy to push change through”.
It’s true that a problem is a great starting point for a DMAIC project – something isn’t working as well as it could. You might prefer to refer to this as an opportunity! Examples include:-
- Too many enquiries that can’t be resolved at first contact
- Too much rework
- Too many complaints
- Steps with long processing times
- Delays between process steps
- …and so on
Starting with a Problem
The problem may be ill-defined to begin with, but by the end of the first of the DMAIC phases – the Define phase – it will be more clearly outlined and its impact and importance understood.
The ‘Problem Statement’ may not sound like the most exciting tool in the Lean Six Sigma toolbox, but it is among the most important! Develop a Problem Statement at the beginning of the Lean Six Sigma project to capture important information on what the problem is, and why it is important to address the problem now. This will provide essential focus and will also serve as a powerful communication tool, helping you to influence stakeholders and gain support.
Rudyard Kipling’s ‘Six Serving Men’ are of great help when it comes to developing Problem Statements.
““I keep six honest serving men
(They taught me all I knew);
Their names are What and Why and When
And How and Where and Who!”
What is it exactly that’s not working? Why is it so important to resolve this issue? When does it happen, and when did it start? How is this problem manifested? Where does it happen? And Who is affected by it? If you can answer these questions within the Problem Statement you are off to a great start!
Note that the cause of the problem is not included in the problem statement. It is important not to jump to conclusions about the causes of the problem – these will be revealed in the Analyse phase. And, in the same way, the solutions are not included. Though some may find it discomforting, it’s fine to have a problem that you don’t have a solution for at this stage.
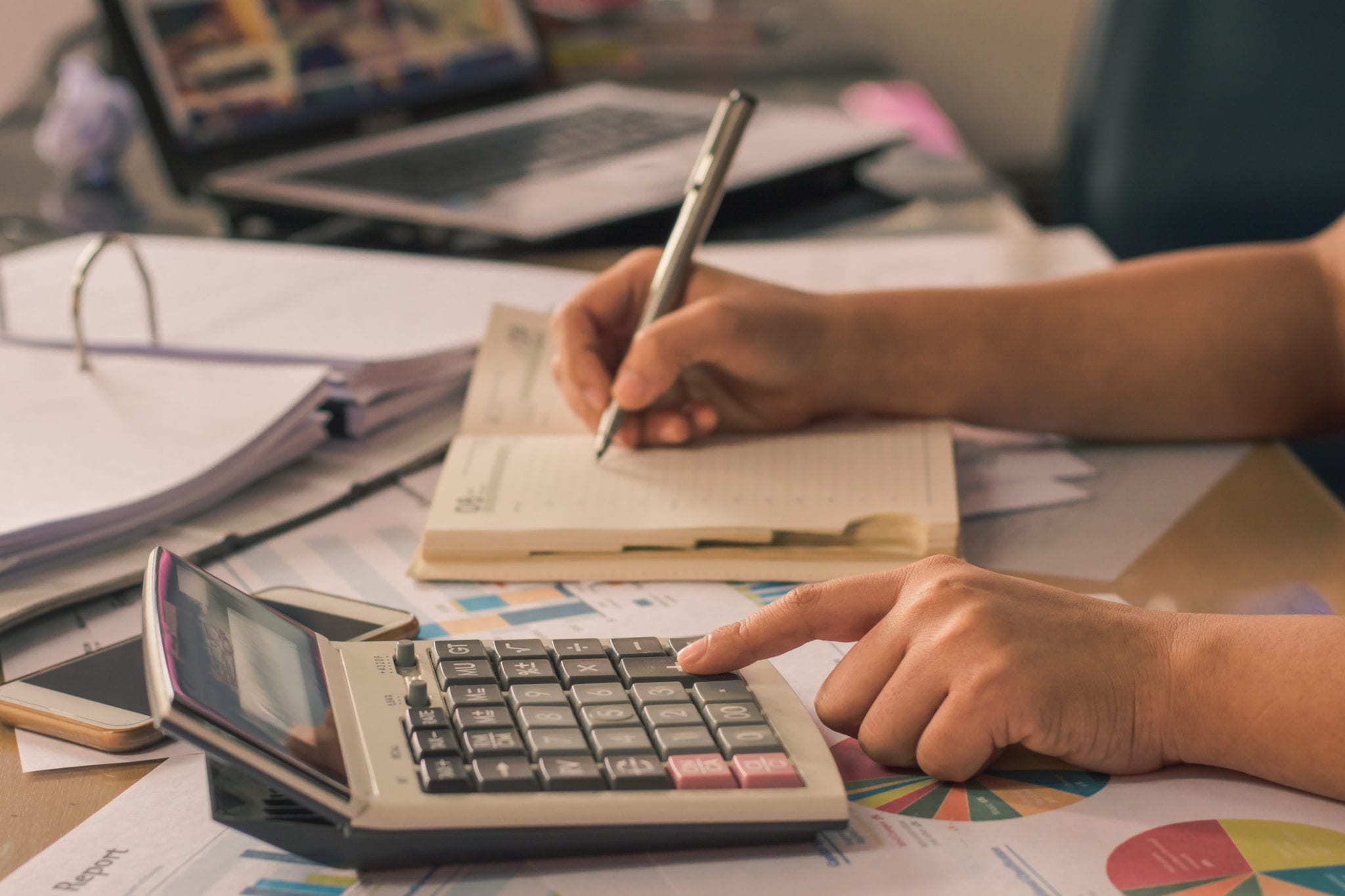
Assigning a Sponsor to the Lean Six Sigma project
It is strongly recommend that any/every Lean Six Sigma project undertaken is supported by a Sponsor or Champion.
This Sponsor should have a level of authority within the organisation that is equal to or bigger than the scope of the project or improvement being undertaken. This allows for effective decision making and leadership. The responsibilities of the Sponsor may include…
- Providing strategic direction for the project team
- Ensuring that the scope of the project is stretching but manageable
- Keeping informed of progress and taking an active role in reviews
- Helping the team overcome roadblocks
- Ensuring appropriate resources are available
- Keeping the team focussed on the desired results
- Sharing project information with others, e.g. leadership team members, steering committees
Establishing the Scope
Small is beautiful when it comes to scoping and scaling Lean Six Sigma improvement projects. Avoid gigantic elephant-eating projects or ocean-boilers – its far better to break things down into manageable chunks and deliver some benefits in a timely fashion than it is to take on too much and fail to deliver anything for 12 months, or never. Remember these wise words from Mark Twain. “Continuous improvement is better than delayed perfection”.
It’s essential to agree what is ‘in’ and what is ‘out’ of scope. This neat tool from the Lean Six Sigma toolbox helps a team to discuss and agree scope – it is called ‘The Frame’.
Simply draw a frame (like the one shown here) on a flip chart and discuss different aspects of the project scope with the team. The discussion areas could include the boundaries of the process to be considered (how wide or narrow is our focus?), the customer segments to include/exclude, the regions, product groups to be addressed, whether IT system changes be in or out of scope etc.
The beauty of The Frame is that everyone can see what has been agreed to be in and out of scope. Any items which are unclear and which end up in the ‘up for discussion’ area need to be directed either into scope or out of scope – they cannot be left unclear. This is something the Sponsor can help with.
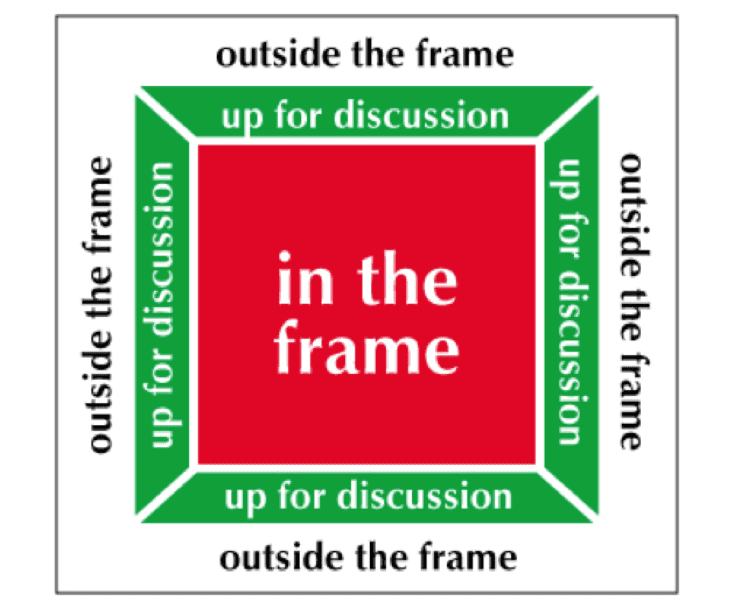
Getting input from the Experts
Lean Six Sigma is as much a people-focussed approach as it is process-focussed. The people involved in processes from day to day have a wealth of knowledge and experience of what works and what doesn’t….what a waste it would be to ignore it. At the start of your Lean Six Sigma project consider who’s input and involvement will be of value – the more the better. Bring a small core team together (teams of about 4 to 6 people work well) and plan for how input from other experts will be included. As Steve Jobs said, “Great things in business are never done by one person. They’re done by a team of people.” Bring together a group of people with the energy to push change through.
The fridge was invented because food wasn’t staying fresh, the light bulb was invented to illuminate darkness, and Les Paul was so fed up that his acoustic guitar sound was being drowned out by other instruments that he electrified it. Dissatisfaction can indeed be a powerful driving force of change. What can we make better?
Feel free to contact us at Catalyst for any help or advice towards your Lean Six Sigma projects.
Jo is a motivated and energetic business improver with extensive experience in developing and deploying Continuous Improvement, Lean Six Sigma, ISO and Excellence strategies across a broad range of organisations and sectors.